How to Seal Hydraulic Fittings: Leak-Proof Techniques
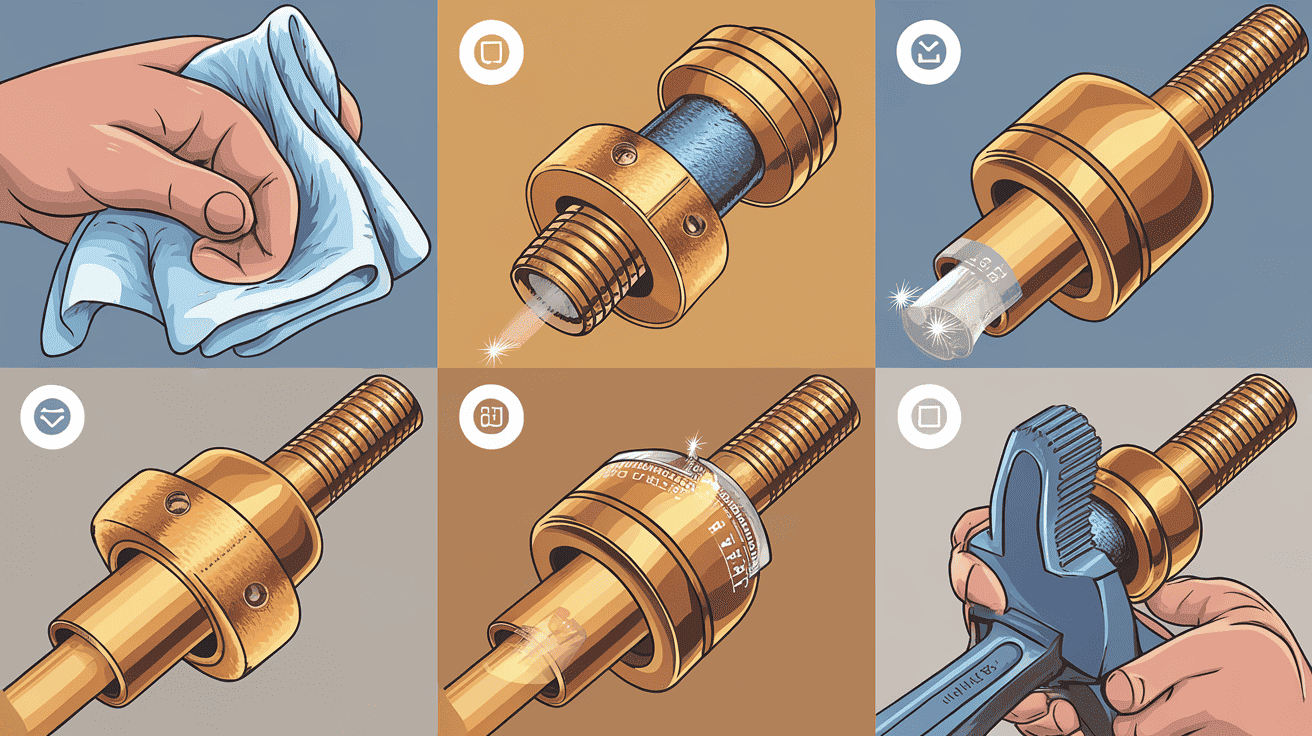
To seal hydraulic fittings, clean all surfaces, then apply thread sealant before tightening. Ensure proper alignment to avoid leaks.
Sealing hydraulic fittings properly is crucial for maintaining an efficient and leak-free hydraulic system. Experts know the importance of starting with a pristine surface, free from any contaminants that could hinder a tight seal. They choose the right type of thread sealant, considering the hydraulic fluid type and the system’s temperature range.
With precision, they align the threads to prevent cross-threading and fasten the fittings to the manufacturer’s recommended torque specification. A carefully sealed hydraulic fitting not only ensures optimal system performance but also extends the lifespan of the hydraulic equipment. This process requires a meticulous approach to avoid future malfunctions and costly repairs.
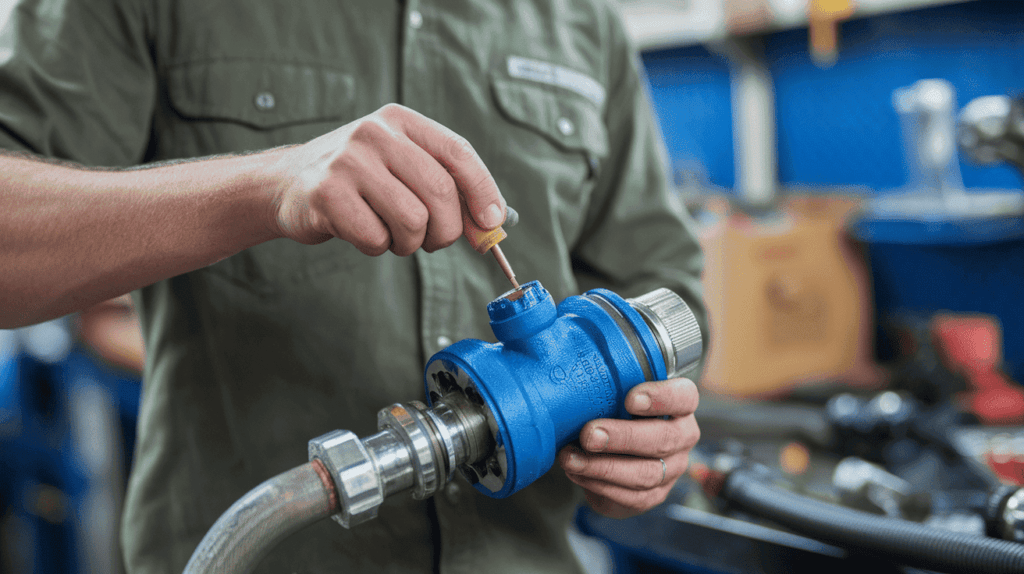
Introduction To Hydraulic Fittings
Hydraulic fittings connect and extend the lengths of pipes and hoses. They are essential in creating powerful, tight connections. These fittings carry fluid between components, so they must remain leak-free to maintain a hydraulic system’s integrity and efficiency.
Understanding Hydraulic Systems
Hydraulic systems use pressurized fluid to power machinery. They include various parts, like pumps, hoses, and fittings.
- Pumps generate the necessary pressure.
- Hoses transport the fluid.
- Fittings secure the connections between hoses and other components.
Importance Of Leak-proof Sealing
Hydraulic fittings must form leak-proof seals to function correctly. Leaks in the system can lead to:
- Decreased equipment performance.
- Potential safety hazards.
- Increased maintenance costs.
Sealing fittings properly is key to preserving system integrity.
Types Of Hydraulic Fittings
Hydraulic fittings are crucial components in various machinery and vehicles. These fittings ensure that hydraulic systems operate efficiently by securely connecting hoses and pipes to transmit fluid under pressure. Identifying the right type of hydraulic fitting is essential for creating a leak-free system. Here’s a closer look at the various types of hydraulic fittings commonly found in hydraulic systems.
Standard Threaded Fittings
Standard threaded fittings utilize threads to make connections. They come in different sizes and thread standards, such as NPT (National Pipe Thread) and BSPP (British Standard Pipe Parallel). Correct thread engagement is imperative to prevent leaks and ensure a strong connection.
Flared Fittings
Flared fittings use a cone-shaped connector and a flared piece of tubing to form a tight seal. They offer extra security and can handle high pressure, making them a go-to choice for critical applications. The flare must be precise to avoid leakage.
O-ring Face Seal Fittings
O-ring face seal fittings feature a flat sealing surface with an embedded O-ring. This design provides superior leak protection in higher-pressure applications. The O-ring must be in good condition and properly fitted to function effectively.
Other Specialized Fittings
- Banjo fittings: Quick to install and remove, excellent for tight spaces
- Swivel fittings: Allow hose rotation to prevent twisting
- Push-to-connect fittings: Easy installation by pushing the tubing into the fitting
Each fitting serves a specific need and offers unique advantages. Always pick the right fitting for your hydraulic system’s requirements.
Preparing To Seal Hydraulic Fittings
Preparing to Seal Hydraulic Fittings is crucial in preventing leaks and maintaining system integrity. The process involves carefully getting your fittings ready. Proper preparation ensures lasting seals and reliable hydraulic connections.
Identifying The Type Of Fittings
Different types of hydraulic fittings exist, each with specific sealing needs. Knowing exactly what kind you are working with is the first step. Common types include O-ring, flared, and face seal fittings. Check for identifying marks or consult the equipment manual.
Cleaning And Inspection
Cleanliness is key in hydraulic systems. First, remove any debris, dirt, or old sealant from the fittings. Use a clean cloth and appropriate cleaner. Inspect each fitting for damage or wear. Discard any fitting that shows signs of damage.
Selecting The Right Sealing Method
Each fitting type may require a different sealing method. Options include Teflon tape, liquid thread sealant, and O-rings. Consider the system’s pressure, temperature, and the hydraulic fluid type. Choose the sealing method that ensures a secure and compatible fit for your specific application.
Sealing Techniques For Threaded Fittings
Working with hydraulic fittings requires careful sealing techniques. Ensuring a tight seal prevents leaks and maintains system integrity. Explore common sealing methods for threaded fittings. Learn their applications and achieve optimal seal performance.
Teflon Tape: When And How To Use It
Use Teflon tape for sealing pipe threads. It’s perfect for water and gas fittings. Follow these steps:
- Clean threads with a brush.
- Wrap tape clockwise. Keep it flat and snug.
- Apply 2-3 layers for best results.
- Reassemble parts and hand-tighten. Then use a wrench for a final turn.
Pipe Dope Application
Pipe dope creates airtight seals. Apply it on male threads. Use a brush or applicator for even coverage.
Steps to apply:
- Clean and dry thread surfaces.
- Spread pipe dope smoothly on threads.
- Join fittings immediately before the dope dries.
- Screw tightly using a wrench, but avoid overtightening.
Anaerobic Thread Sealants
Anaerobic sealants cure in the absence of air. Ideal for high-pressure systems.
- Ensure thread cleanliness.
- Apply sealant evenly.
- Assemble parts right after application.
- Allow cure time as per product instructions.
Torque Wrench Usage For Proper Tightening
Use a torque wrench for precision. Follow these steps:
- Select appropriate wrench size for fitting.
- Set torque value based on fitting size and type.
- Apply steady pressure to reach desired torque.
- Confirm torque specification. Avoid over-tightening.
Sealing Flared And O-ring Face Seal Fittings
Sealing Flared and O-Ring Face Seal Fittings is crucial for the proper function of hydraulic systems. High-quality seals prevent leaks and ensure system integrity. This guide focuses on effective techniques for sealing these specific types of fittings.
!– Proper Installation Of Flared Fittings —
Correct installation is vital for flared fittings. Follow these steps:
- Inspect the flare for damage or imperfections.
- Clean all surfaces before assembly.
- Align the fitting and tube carefully.
- Tighten the nut by hand until it meets resistance.
- Use a wrench to finalize the seal without over-tightening.
!– Importance Of O-ring Lubrication —
Lubricate O-rings to:
- Ensure a smooth seal without damage.
- Prevent O-ring twisting or tearing during installation.
- Reduce friction and wear over time.
!– Precision Alignment To Prevent Leaks —
Alignment is key to avoid leaks. Use these tips:
- Check alignment with a gauge if available.
- Adjust the fitting to prevent stress on the connection.
- Inspect after installation for any signs of misalignment.
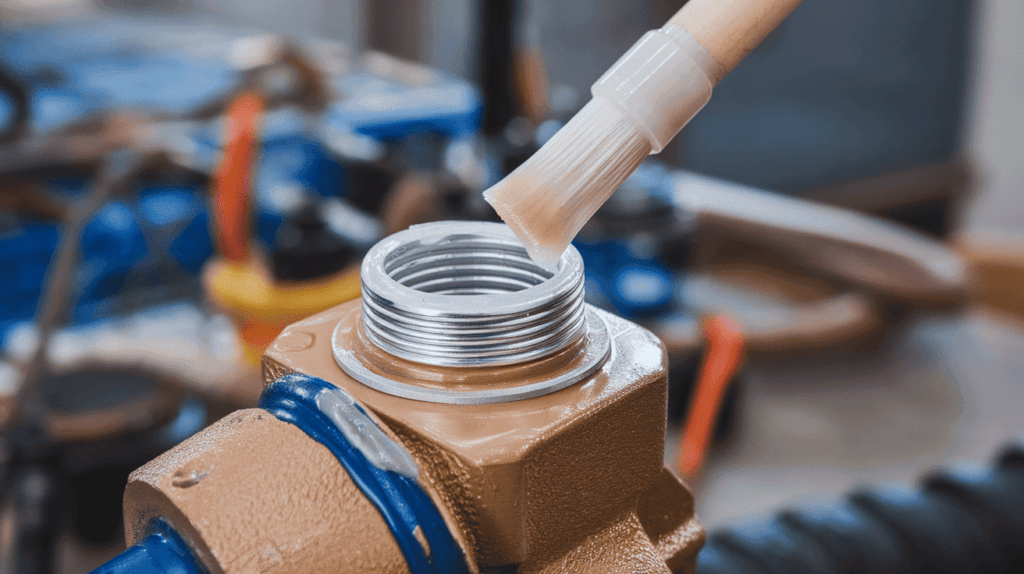
Testing And Maintenance Of Sealed Fittings
Keeping hydraulic systems in top shape is critical. It starts with ensuring that all hydraulic fittings are securely sealed. A reliable sealing prevents leaks and maintains system pressure. Regular testing and maintenance is vital. This ensures longevity and optimal performance of hydraulic fittings.
Pressure Testing For Leak Detection
Pressure testing is a reliable method for checking sealed fittings. This process involves applying pressure to a system to verify that there are no leaks present. Use the following steps for effective pressure testing:
- Isolate the segment to be tested.
- Apply the specified pressure.
- Monitor for consistent pressure levels.
- Inspect for any signs of fluid escape.
Scheduled Maintenance And Leak Inspection
Planned maintenance keeps systems functioning. It prevents unexpected failures. Here’s what to include in a regular maintenance schedule:
- Clean surfaces around fittings to spot leaks.
- Check for signs of corrosion or damage.
- Verify that fittings are tight and secure.
- Inspect hoses for any signs of wear or fatigue.
Replacing Fittings And Seals When Necessary
During inspections, sometimes you’ll find fittings or seals that need replacement. Here’s what you need to consider:
- Identify damaged seals and fittings early.
- Replace with the correct type and size.
- Ensure new fittings are properly aligned.
- Test the system after replacements.
Troubleshooting Common Sealing Issues
Troubleshooting common sealing issues in hydraulic fittings is crucial for maintaining efficient system operation. Getting to the root of leaks and correcting improper sealing techniques ensures longevity and performance.
Diagnosing The Source Of Leaks
Identifying where a hydraulic system is leaking can be tricky.
- Clean the area around fittings.
- Use dye or fluid to spot the leak’s origin.
- Check the seal’s surface for damage or irregularities.
Rectifying Incorrect Sealing Techniques
Improper sealing might cause issues. Follow these steps to fix:
- Remove and inspect the fitting.
- Ensure surfaces are clean and undamaged.
- Apply the correct sealant type.
- Reassemble according to manufacturer’s guidelines.
Dealing With Wear And Tear Over Time
Regularly inspect fittings for signs of wear and tear.
Issue | Action |
---|---|
Cracks in the seal | Replace the seal |
Corrosion on metal parts | Apply anti-corrosive treatment or replace the part |
Hardened elastomers | Install new elastomeric seals |
Regular maintenance schedules prevent unexpected leaks and failures.
Safety And Best Practices
Hydraulic systems power many machines, big and small. Sealing hydraulic fittings is crucial to their safe and efficient operation. Knowing the right practices and safety measures can prevent accidents and ensure longevity.
Understanding The Hazards Of Hydraulic Leaks
Hydraulic leaks pose risks to both machines and workers. High-pressure fluid can cause injury. Fluid leaks may lead to slippery surfaces, creating fall hazards. It is vital to recognize these dangers to maintain a safe environment.
Adhering To Safety Protocols
- Wear proper PPE such as gloves and eye protection.
- Follow the equipment’s manual for correct procedures.
- Use the right tools for the fittings in use.
- Perform regular maintenance checks.
Attention to detail saves lives and equipment.
Continuous Learning And Training
Regular training keeps teams sharp. It includes updates on safety practices and new hydraulic technologies. A well-trained team can handle leaks and fitting issues swiftly and safely.
Topic | Focus Area |
---|---|
Sealing Techniques | Latest methods to seal effectively. |
Safety Updates | Current best practices for safety. |
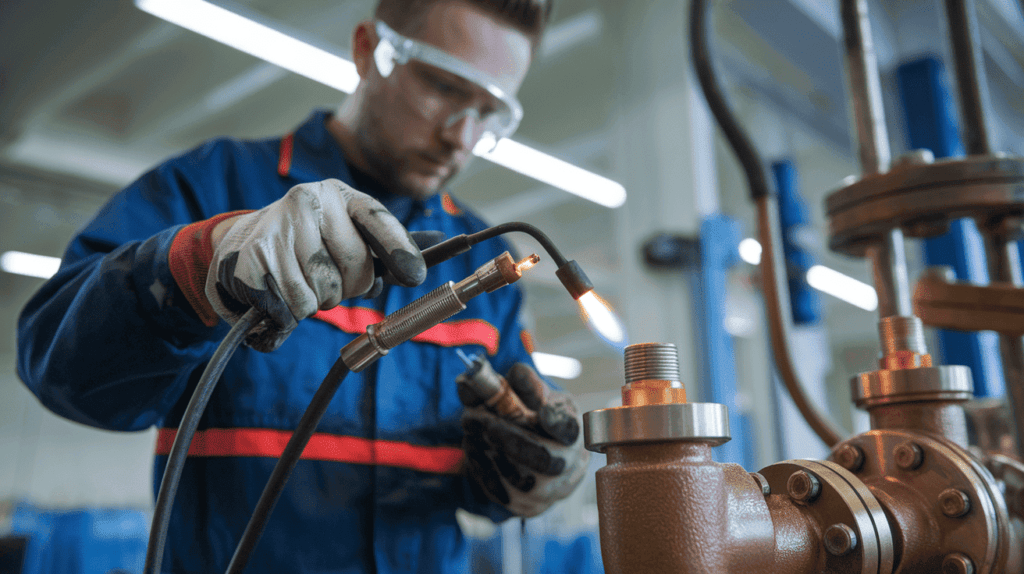
Frequently Asked Questions Of How To Seal Hydraulic Fittings
What Is The Best Sealant For Hydraulic Fittings?
The best sealant for hydraulic fittings is typically a high-quality PTFE tape or a liquid thread sealant designed for high-pressure systems.
How Do You Stop A Hydraulic Fitting From Leaking?
To stop a hydraulic fitting from leaking, ensure proper installation, use the correct fitting and sealant, tighten to the manufacturer’s specifications, regularly inspect for wear, and replace damaged components promptly.
Should You Put Teflon Tape On Hydraulic Fittings?
No, Teflon tape is not typically recommended for hydraulic fittings; instead, use the proper thread-sealing compound designed for hydraulic systems.
How Do You Seal High Pressure Threads?
To seal high-pressure threads, clean and inspect the threads, apply a high-quality thread sealant, screw the components together tightly, and confirm the seal with a pressure test. Always follow the sealant manufacturer’s instructions for best results.
What Causes Hydraulic Fitting Leaks?
Improperly sealed hydraulic fittings often lead to leaks, commonly caused by incorrect installation, worn threads, or damaged O-rings and seals.
Conclusion
Securing hydraulic fittings is crucial for system integrity. Adopt these practices to avoid leaks and maintain pressure. Remember, selecting quality seals and proper installation techniques extend equipment life. For optimal performance, regular checks are indispensable. Seal smart, maintain well, and ensure your hydraulic systems run at peak efficiency.
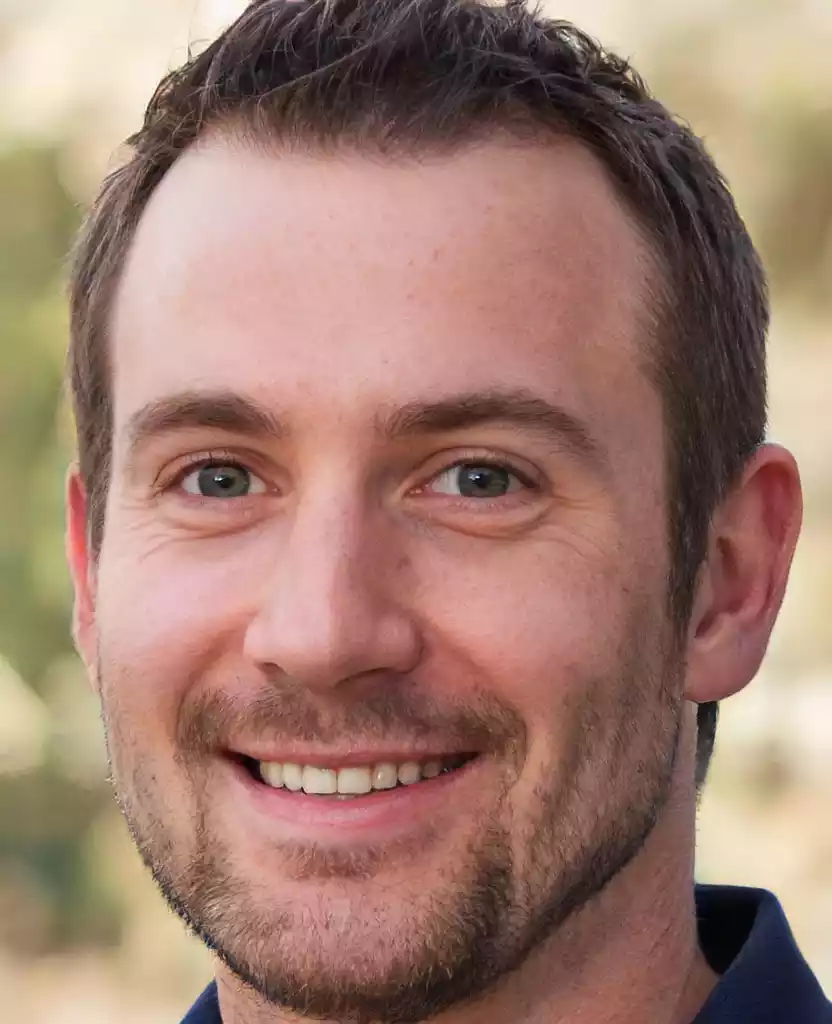
I am Robert Sandin, a professional sealing expert with a diverse range of expertise. From concrete to various other materials, I possess in-depth knowledge and experience in the art of sealing. On my website, I offer valuable tips and expert recommendations on sealing techniques and products for different materials. Whether it’s concrete, wood, metal, or more, I am committed to providing you with the guidance you need for successful sealing projects.